Imagine a rod in the grill of your home is rusted, or a part of the entrance gate is damaged due to weather conditions. What will you do? Will you replace the entire grill or gate?
Isn’t it the best idea to repair the metal grill or gate part with a new piece of metal rather than replacing the entire structure? This is the situation where the process of welding comes into the picture. We see fabrication shops on all streets of the area. Have you ever thought about what they do?
Yes, you are right. They do welding.
Welding helps in joining two metals at a high temperature by melting the base metal and the filler metal. Let us know more about welding, its types, advantages and disadvantages in this article.
What is Welding?
Welding is a fabrication process that lets you join materials like metals by using heat at high temperatures. Welding uses high temperature to join the materials, whereas soldering and brazing do not allow the base metal to melt. After cooling, the base metal and the filler metal get attached.
The welding process came to light when there was a search for the technique for developing iron into useful shapes. Welded blades were the first result of welding in the early years—the carburization of iron produced hard steel that was very brittle for usage. Later interlaying the rigid and soft iron with high-carbon material and hammer forging resulted in a tough and durable blade.
The process of welding uses filler material. The filler material is the pool of molten material that aids in the formation of a strong link between the base metal. The shielding process after welding the metals protects both the base and filler components from being oxidised.
From gas flame to ultrasound, many energies are used in welding like electron beams, electric arc, LASER, and friction. Now let us understand various types of welding.
Types of Welding
There are many types of welding used for various purposes under different situations. They are:
Manual welding includes:
- Forge welding
- Arc welding
- Oxy-fuel welding
- Shielded metal arc welding
- Gas metal arc welding
- submerged arc welding
- flux-cored arc welding
- electroslag welding
- Laser beam welding
- electron beam welding
- magnetic pulse welding
- friction stir welding
Forge Welding
Forge welding is the early version of welding where it was used to join the small iron pieces to make larger valuable pieces. It is the simplest welding method where two metals are heated and joined, and later hammered for the finishing purpose.
Arc Welding
Arc welding is the most common type of welding seen today. Arc welding is a type of welding in which an electric arc is created to heat and join metals. Tiny globules of molten metal are transferred from the metal electrode to the weld joint.
Oxy-Fuel Welding
Oxy-fuel welding is oxy welding, gas welding, or oxy acetylene welding. This process uses the combustion of fuel gases like acetylene and oxygen to weld or cuts the metals. Edmond Fouché and Charles Picard, French engineers in 1903, developed Oxy-fuel welding.
When acetylene and oxygen are mixed in proper measures inside the hand-held torch or blowpipe, the hot flame is produced in the hand-held torch measuring 3,200 degrees Celsius. The flame’s intensity can be manipulated by altering the proportion of the volume of oxygen to acetylene. Welding can be done using this flame.
Shielded Metal Arc Welding
Various names like flux shielded arc welding, manual metal arc welding, or stick welding are known as shielded metal arc welding. It is a manual welding process that uses an electrode covered with flux to perform welding.
AC or DC power supply forms an electric arc between the electrode and the metals to be joined.
Gas Metal Arc Welding
Gas metal arc welding in which an electric arc is formed between a consumable metal inert gas wire electrode and the workpiece metal. The generated heat melts the workpiece metal and is then joined. It is a semi-automatic or automatic process which uses AC or DC from the power supply.
Submerged Arc Welding
Submerged arc welding is a type of arc welding process that involves forming an arc between the electrode and the workpiece. A blanket of granular fusible material shields the arc on the work.
Flux-Cored Arc Welding
Flux-cored arc welding is a semi-automatic or automatic arc welding process. Flux-cored arc welding is similar to the metal active gas welding process. It uses a continuous wire fed electrode and a constant-voltage welding power supply.
Electroslag Welding
Electroslag welding is the most effective welding used to weld materials more significant than 25 mm up to about 300 mm. In electro slag welding, heat is generated by passing electricity between the filler metal and the workpiece through a molten slag covering the weld surface.
Laser Beam Welding
Laser beam welding is the process in which the metal or thermoplastic materials are joined together with the aid of LASER (Light Amplification by Stimulated Emission of Radiation). It is an efficient technique that can perform deep welds. Laser beam welding is a non-contact process requiring access to the weld zone from one side of the welded parts. Since the LASER beam is monochromatic and single phased, without any divergence, high energy light produced is channelised to perform welding.
Electron Beam Welding
Electron beam welding is a technique in which high-velocity electrons are applied to the materials to be welded. Electron beam welding is undertaken under vacuum conditions to prevent dissipation of the electron beam. The kinetic energy from the electrons is transformed into heat, and the materials are welded. The electron gun is used to generate electrons, and the electron gun helps control the flow of the electrons. Electron beam welding is performed in a vacuum condition to avoid the scattering of electrons.
Magnetic Pulse Welding
Magnetic pulse welding is a technique that uses magnetic force to weld two materials together. It is the solid-state welding developed in 1970 and is used extensively in automotive industries. It is the fastest way of welding, which consumes only microseconds without the need for welding consumables or shielding gases.
Friction Stir Welding
Friction stir welding is also a solid-state welding process that uses frictional heat generated by a rotating tool to join materials.
The tool, equipped with a profiled probe and shoulder, is rotated and plunged into the interface between two workpieces. The tool, when moved along the joint line, causes the material to heat and soften. The shoulder also acts to contain this plasticized material, which is mechanically mixed to create a solid phase weld.
Advantages and Disadvantages of Welding
Advantages
- Welding establishes strong, durable, and permanent joint links.
- It is a simple process that results in a great finish.
- The technique, when used with filler material, produces a stronger weld than the base material.
- It can be performed at any place
- It is an economical and affordable process
- It is used in various sectors like construction, automobile, and many more industries.
Disadvantages
- It is hazardous when performed under the safety and security guidelines.
- It is a difficult task to dismantle the joined material through welding.
- Requires skilled labor and electric supply.
Hope you have learned what is welding and its types. Visit BYJU’S – The Learning App to know more about various interesting and engaging concepts.
Related links | |
Electricity And Magnetism | Mechanical wave |
Acoustic | Sound wave propagation |
Frequently Asked Questions on Welding
1. What is welding?
Welding is joining two materials like thermoplastics or metals at a high temperature by melting the base material and filler metal.
2. What is meant by LASER?
LASER is a device that emits high-intensity monochromatic light through optical amplification based on the stimulated emission of electromagnetic radiation.
3. What is filler material?
The filler material is the pool of molten material that aids in the formation of a strong link between the base metal.
4. Which is the early method of welding?
Forge Welding.
5. List the advanced methods of welding
- Laser beam welding
- electron beam welding
- magnetic pulse welding
- friction stir welding
What are the Physical Properties of Metals and Non-metals that differentiate them from each other?
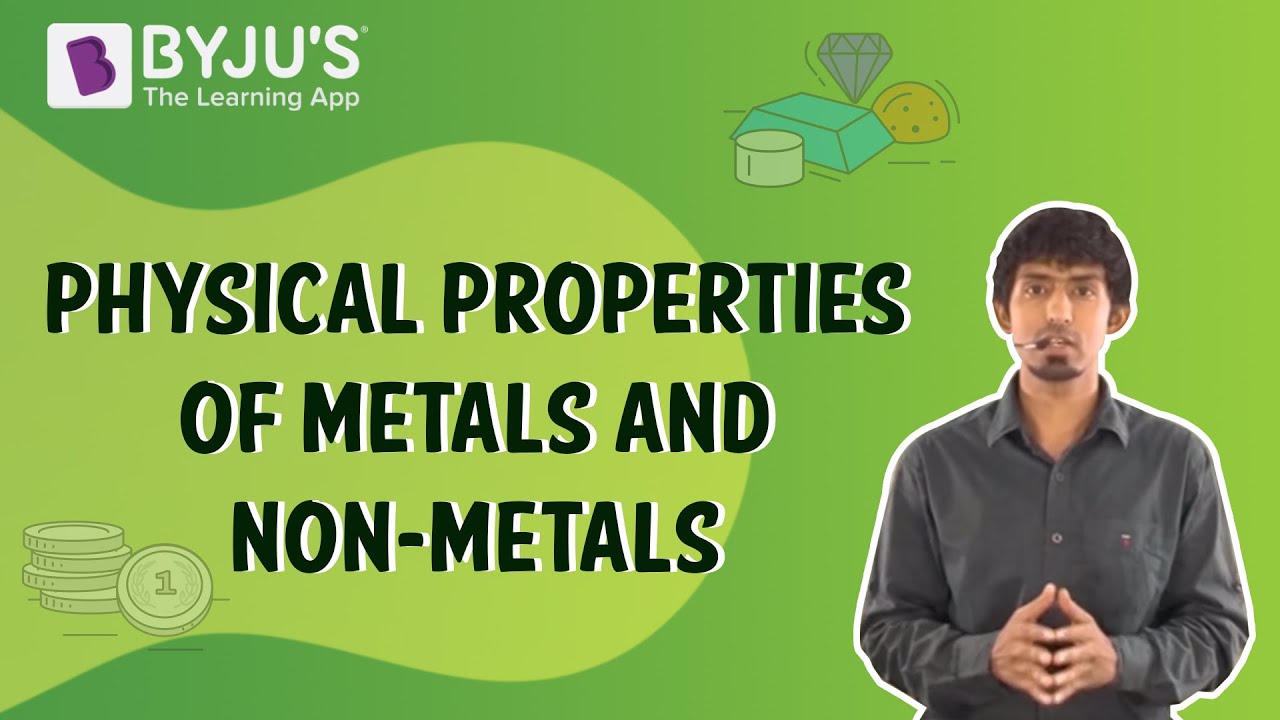
Comments