What is Thermosetting Polymer?
A thermosetting polymer which is also known as a thermoset or thermosetting plastic is a polymer consisting of cross-linked structure or heavily branched molecules.
These polymers which are in the soft solid or viscous state on heating undergo extensive cross-linking in moulds and become irreversibly hard as well as insoluble products.
Recommended Videos
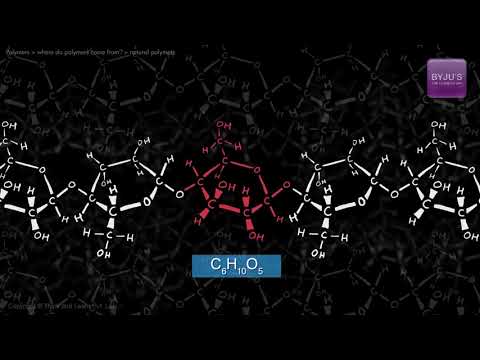
Properties of Thermosetting Polymers
- One of the main properties of thermoset plastics or polymers is that they harden during the moulding process and after solidifying they cannot be softened.
- Typically, when the polymers are moulded and shaped they acquire a three-dimensional cross-linked structure along with strong covalent bonds that further help them retain their strength as well as a structure even if the temperatures are set high.
- However, thermoset plastics are brittle and tend to char and burn if heat is applied for a prolonged state. Normally, thermosets decompose before melting. Meanwhile, thermoset resins are insoluble in most of the inorganic solvents.
Thermosetting Process
Processing thermoset polymers usually involve three stages.
- The first stage is commonly referred to as resole where during this stage the resin is an insoluble and fusible condition or state.
- In the second stage, the thermosets are only partly soluble, and they tend to display the characteristics of a thermoplastic where the changes are reversible.
- However, this is a temporary state as the molten form of thermoset lasts only for a short time because the increase in temperatures promotes cross-linking.
- The final stage is where the cross-linking reaction occurs and the final structure of thermosets is constructed. This mostly involves the moulding phase which is conducted under controlled temperature and some application of pressure.
- The final product will have a three-dimensional internal network structure consisting of highly cross-linked polymer chains. At this point, the product cannot be thermally deformed.
In addition, thermoset plastics can also be processed via a single-stage method called reaction injection moulding (RIM). While this process is similar to the method described above the only distinction here are that polymers are combined during the curing process to form a permanent chemical bond. The process basically uses polymerization in the mould instead of cooling to facilitate the formation of a solid polymer.
Some common methods of moulding thermosets include:
- Extrusion moulding which is used for making insulation for electrical cables, threads of fabric and pipes.
- Compression moulding is used to give shape to BMC and SMC thermosetting plastics.
- Spin casting which is a process mainly used for the production of figurines, fishing lures and jigs, emblems and even replacement parts.
Examples
- One of the most common examples of thermosets is bakelite which is relatively a bad conductor of electricity and heat.
- It is mainly used for making electrical switches, handles of various utensils, etc.
- Another example is Melamine which has a capacity to resist fire and heat much efficiently than other plastics.
- It is used in kitchenware and fabrics as well as floor tiles.
- Some other examples of thermoset plastic polymers include silicones, vulcanized rubber, epoxies, polyesters and phenolics.
Thermosetting Plastic Advantages and Disadvantages
- Some main advantages of thermosetting plastics include – they are more resistant to high temperatures, they have high levels of dimensional stability, are cost-effective, and allow highly flexible design.
- On the other hand, some thermosetting plastics disadvantages include, the products can not be recycled or reused and the products cannot be remoulded or reshaped.
Comments