Aluminium is a soft, silvery-white, corrosion-resistant metal. It is the most abundant metal in the earth’s crust as it makes up 8% of the crust and it is the third most abundant element after oxygen and silicon. Bauxite ore (Al2O3.xH2O) is the major source of aluminium till date which is a mixture of hydrated aluminium oxide.
Aluminium can also be recovered from cryolite (Na3AlF6) and alunite. It is also found in gemstones such as garnet, topaz and chrysoberyl. The chemical symbol of this metal is Al. In the boron group with symbol Al, aluminium is a chemical element and is the most commonly used non-ferrous metal.
Table of Contents
Aluminium Ore
Ores of Aluminium
Aluminium is a highly reactive metal, belonging to the IIIA group of the periodic table. In nature, aluminium is found in the form of its oxide in its ores. The important ores of aluminium are
-
-
-
- Bauxite – Al2O3.2H2O
- Corundum – Al2O3
- Cryolite – Na3AlF6
-
-
Metallurgy of Aluminium
Aluminium is mostly extracted from its bauxite ore.
Dressing of Ore
The ore is mechanically crushed and pulverized.
Concentration of ore
The bauxite ore contains ferric oxide and silica as impurities. Gravity separation removes silica from crushed ore and magnetic separation separates ferric oxide impurities from the ore. The ore is then concentrated by a chemical process.
Bauxite is the name given to aluminium ore. To generate aluminium oxide, bauxite is purified, a white powder from which aluminium can be extracted. Aluminium oxide has a very high melting point of more than 2000° C which makes melting very expensive. Aluminium oxide in water does not dissolve, but in molten cryolite, it dissolves.
Pure aluminium is a silver-white metal with many desirable features. It’s light, non-toxic, non-magnetic, and non-sparking. It’s a bit ornamental. It’s created, machined, and cast readily. Pure aluminium is soft and lacks strength, but it has very helpful characteristics for alloys with tiny quantities of copper, magnesium, silicon, manganese and other components.
Bayer’s Process
Here aluminium is treated with concentrated sodium hydroxide solution to form soluble sodium aluminate which can be filtered off. The filtrate is heated with water to get aluminium hydroxide which on strong heating gives alumina.
Hall-Heroult Process
The Hall-Heroult process is widely used in the extraction of aluminium. In Hall-Heroults process, pure Al2O3 is mixed with CaF2 or Na3AlF6. This results in lowering the melting point of the mixture and increases its ability to conduct electricity. A steel vessel with a lining of carbon and graphite rods is used.
The carbon lining acts as a cathode and graphite act as an anode. When electricity is passed through the electrolytic cell which consists of carbon electrodes oxygen is formed at the anode. This oxygen formed reacts with the carbon of the anode to form carbon monoxide and carbon dioxide. In this method of production of aluminium, for every 1 kg of Al produced, approximately 0.5 Kg of carbon anode is burnt.
Aluminium ions are created at the adverse cathode from the aluminium oxide and then sink down because they are heavier than the cryolite solution. Then, the liquid shape of the aluminium that has sunk to the bottom. On the other side, at the positive anode, the oxygen from the aluminium oxide forms and responds to carbon dioxide CO2 with the graphite carbon.
The overall reaction is:
2Al2O3 + 3C → 4Al + 3CO2
The electrolytic reactions are:
At the cathode:
Al 3+ + 3e– → Al (l)
At the anode:
C (s) + O2- → CO (g) + 2e–
C (s) + 2O2- → CO2 (g) + 4e–
During the process of electrolysis,
-
-
-
- Aluminium ions that are positively charged gain electrons from the cathode and form molten aluminium.
- Oxide ions lose electrons at the anode and form molecules of oxygen.
-
-
In the electrochemical sequence i.e., reactivity series, aluminium is very reactive to be removed from its ore by carbon reduction. The required temperatures are too high to be economical.
Aluminium Uses
The list of uses of aluminium is given below.
-
-
-
- Aluminium is used in a wide range of applications in the field of transport, construction, etc.
- Aluminium foils are used in the food industries for wrapping food.
- The dust of this metal is used in paints.
- It is used in the extraction of manganese and chromium from its oxides.
- As it is a soft metal and can be moulded into any shape it is used in the manufacturing of storage cans.
- After iron, aluminium is the most commonly used metal.
- It is mostly used with another metal in an alloy, meaning that it is blended with another metal to create another compound with some desirable characteristics-like stainless steel.
- Aluminium being light, a good conductor of heat, corrosion-resistant and cheap is used in making household appliances.
- It is used in electric transmission as it is a good conductor of electricity.
-
-
Recommended Videos
Froth Floatation
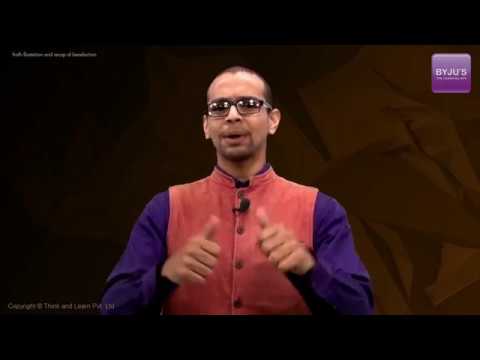
Electrometallurgy
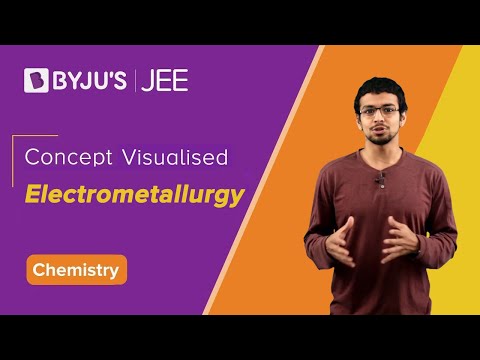
Frequently Asked Questions – FAQs
How is Aluminium extracted from its ore?
Bauxite is an important ore of aluminium. Bauxite is crushed, leached and then subjected to electrolysis to get aluminium.
Why is Aluminium extracted from alumina?
Aluminium is more reactive than carbon and has more affinity towards oxygen. So aluminium can not be reduced by using carbon. Electrolysis is the best method for extraction.
What are the properties of Aluminium?
Pure aluminium has high electrical conductivity and is flexible, ductile, corrosion-resistant. Aluminium is being used in an ever-increasing number of applications by using various combinations of its advantageous properties such as strength, lightness, corrosion resistance, recyclability, and formability.
What are the types of Aluminium?
There are two main classifications, casting alloys and wrought alloys, both further subdivided into the heat-treatable and non-heat-treatable categories. Approximately 85% of aluminium is used for wrought items, such as rolled metal, foils and extrusions.
Why is Aluminium ore purified?
Ore is a chemical substance in which metal is in the combined form along with gangue. Bauxite is an ore of aluminium which is hydrated aluminium oxide along with impurities. To get pure aluminium from aluminium ore, the purification process is done.
Can Aluminium be extracted by smelting?
Smelting is a process by which metal is obtained from its ore by using heat and a reducing agent. Being electropositive, aluminium has a high affinity for oxygen and can not be extracted through smelting.
For detailed information on the Extraction of Aluminium: Ores and Minerals, download BYJU’S – The Learning App.
Thank you Byju’s for this