What Is Polymerization?
Polymerization is a process through which a large number of monomer molecules react together to form a polymer. The macromolecules produced from a polymerization may have a linear or a branched structure. They can also assume the shape of a complex, three-dimensional network. There exist several categories of polymerization reactions; the most important ones are step-growth polymerization, chain-growth polymerization (both fall under the category of addition polymerization), and condensation polymerization.
Download Complete Chapter Notes of Polymers
Download Now
A polymer is a substance that is made up of very large molecules that are, in turn, made up of many repeating units called monomers. Polymerization is the process through which these monomers come together to form the macromolecules that constitute polymers. An illustration detailing the polymerization of the monomer styrene into the polymer known as polystyrene is provided below.
Depending on the functional groups present in the reacting monomers, the complexity of the mechanism of the polymerization reaction may vary. The most simple polymerization reactions involve the formation of polymers from alkenes via free-radical reaction. Polyethylene, which is one of the most commercially important polymers, is prepared through such a polymerization process (the reactant monomer used here is ethylene).
It should be noted that polymerizations involving only one type of monomer are called photopolymerization, whereas those involving more than one type of monomer are called copolymerization processes. In simple words, we can describe polymerization as a chemical process that results in the formation of polymers or the process of creating polymers. When polymerization occurs, the smaller molecules, which are known as monomers via chemical reaction, are combined to form larger molecules. A collection of these large molecules form a polymer. The term polymer, in general, means “large molecules” with higher molecular mass. They are also referred to as macromolecules.
Table of Contents
- Step Growth Polymerization
- Condensation Polymerization
- Chain Growth Polymerization
- Preparation of Polymers
- Classification of Polymerization
Polymers are formed by the addition of a network of structural units or monomers, as mentioned above. The interesting part is that these are reactive molecules and are usually linked to each other by covalent bonds. These monomers add together to form a long chain to form a product with specific properties. This whole process of the formation of polymers is called polymerization. Polythene and Nylon 66 are some examples of polymers.
Mechanism of Polymerization
Generally, polymerization consists of three steps which include initiation, propagation, and termination. As for the reaction mechanism, the process of polymerization mainly involves two different methods, the step-growth mechanism and the chain-growth mechanism.
Step Growth Polymerization
In step-growth polymerization, the polymers are formed by the independent reaction between the functional groups of simple monomer units. In step-growth, each step may consist of a combination of two polymers having a different or the same length to form a longer-length molecule.
The reaction is a lengthy process, and the molecular mass is increased at a very slow rate. An example of step-growth polymerization is condensation polymerization, where a water molecule is evolved in the reaction when the chain is lengthened.
In condensation polymerization, the formation of the polymer occurs when there is a loss of some small molecules as byproducts through the reaction, where molecules are joined together. The byproducts formed may be water or hydrogen chloride. Polyamide and proteins are examples of condensation polymers.
Some of the different types of condensation polymerization are given below.
Polyamides
They are synthetic fibres and are called nylons. These polymers have an amide linkage between them. Condensation polymerization of di-amines with di-carboxylic acid and also of amino acids and their lactams will create a polyamide.
- Nylon 66: This polymer is prepared under the condition of high pressure and temperature by the condensation polymerization of hexamethylenediamine with adipic acid.
- Nylon 6: It is prepared by heating caprolactam with water under high temperatures. It is used for tyre cords, fabrics and ropes.
Polyesters
When dicarboxylic acids and diols undergo polycondensation, polyesters are formed. They are prepared by heating a mixture of terephthalic acid and ethylene glycol at 460 k by using zinc acetate antimony trioxide as a catalyst. Dacron or terylene are the best-known examples of polyesters. And also they are used for glass reinforcing materials in safety helmets.
Phenol-Formaldehyde Polymer
These are the old synthetic polymers obtained by condensation polymerization of phenol with formaldehyde in the presence of either an acid or base as a catalyst.
Novolac, on heating with formaldehyde, undergoes crosslinking and forms an infusible sold mass named as Bakelite. They are used for combs, electric switches and phonograph records.
Melamine-Formaldehyde Polymer
It is formed by the condensation polymerization of melamine and formaldehyde in certain conditions. They are used for the manufacture of unbreakable crockery.
Chain-Growth Polymerization
In chain-growth polymerization, the molecules of the monomers are added together to form a large chain. The monomers added may be the same type or different. Generally, alkenes, alkadienes and their derivatives are used. In this mode, the lengthening of chains occurs as a result of the formation of either free radicals or ionic species.
Free Radical Mechanism
Many of the monomers, like alkenes or dienes and their derivatives, are polymerized in the presence of free radicals. The polymerization of ethene to polythene is by heating or exposing it to light by using a small amount of benzoyl peroxide initiator. The phenyl free radical formed by peroxide is added to the ethene double bond and hence forms a new larger free radical.
Also Read: Chemical Bonding
It is called a chain initiation step. This newly formed radical will react with another molecule of ethene to form another new free radical, and so on. This repeated formation of a new free radical is called chain propagation. Finally, at some stage, the polymerized product will be formed, and this step is called a chain termination step. The steps are detailed below.
The three steps followed by a free radical mechanism:
Polymerization Chemical Reaction
When we talk about polymerization chemical reactions, we basically refer to a polymerization reaction of organic monomers. These monomers are in a solution, which further consists of particles that will be coated with the formed polymer deposited on the particle surface. This leads to the formation of a coating layer. The reaction includes either monomer adsorption polymerization or emulsion polymerization.
Preparation of Polymers
Polyethene
There are two types of polyethylenes, and they are given below:
1. Low-Density Polyethene
This type of polymer is obtained by the polymerization of ethene under the condition of high pressure of 1000 to 2000 atmospheres at 350 to 520 k temperature in the presence of dioxygen or peroxide initiator as a catalyst in a very small amount.
It is formed through the free radical addition and H-atom abstraction, having a highly branched structure. It is chemically inert in nature and tough but flexible. It is a poor conductor of electricity. LDP is used for the manufacture of toys, squeeze bottles and flexible pipes.
2. High-Density Polyethene
It is prepared by the polymerization addition of ethene in the presence of a catalyst like triethyl aluminium and titanium tetrachloride. The process takes place in a hydrocarbon solvent, in a condition of low pressure of 3 to 4 atmospheres and 343 k temperature.
Like the LDP, it is chemically inert but comparatively tougher and harder. It is used for the manufacture of buckets, dustbins, pipes, etc.
Polytetrafluoroethylene
It is also known as Teflon and is manufactured by heating tetrafluoroethylene with a free radical at high pressure. Teflon is chemically inert and less corrosive due to its resistive property against corrosive agents. It is used for gaskets and non-stick surface-coated utensils.
Polyacrylonitrile
This polymer is formed by the addition polymerization of acrylonitrile in the presence of a peroxide catalyst. It is used as a substitute for wool in the making of commercial fibres such as Acrilan.
Anionic Polymerization
It is an addition polymerization that involves the polymerization of monomers that are initiated with anions. This polymerization will be initiated by the transfer of electrons from the ion to the monomer.
The initiators used may be weakly nucleophilic if the monomer is highly electrophilic. In the propagation, the complete consumption of monomer occurs, and this will be faster even at low temperatures. Generally, vinyl monomers are polymerized by this method. It is very sensitive to the solvent used in the reaction. This method is used for the production of synthetic polydiene rubbers, SBR and thermoplastic styrene elastomers.
Classification of Polymerization
Polymers are classified into different categories based on several factors such as source, structures, mode of polymerization, molecular forces and growth of polymers. Let’s discuss them in detail below.
Based on Source
Polymers are again divided into three subcategories:
- Natural polymers: They are found naturally in plants and animals. Resins, starch and rubber are examples of this.
- Semi-synthetic polymers: This is a modified version of natural rubber; rubbers are treated with chemicals to make them semi-synthetic. Cellulose acetate and cellulose nitrate are examples that come under this subcategory.
- Synthetic polymers: Polymers which are completely man-made are called synthetic polymers. Polythene, Nylon 66, and synthetic rubber are the widely used synthetic polymers.
Based on the Structure of Polymers
There are three different types polymers, based on their structure:
- Linear polymers: They consist of a long and straight-chain of monomers. PVC is a linear polymer
- Branched polymers: They are linear polymers containing some branches. Low-density polythene is an example.
- Network or cross-linked polymer: Polymers having cross-linked bonds with each other is called cross-linked or network polymer. Generally, they are formed from bi-functional or tri-functional monomers. Bakelite and melamine are examples of this type of polymer.
Based on the Mode of Polymerization
Based on the mode of polymerization, they are divided into two subcategories:
- Addition polymers: Polymers formed by the repeated addition of monomers by possessing double or triple bonds are called addition polymers. If the addition is of the same species, they are called homopolymers, and if the addition is of different monomers, they are called copolymers. Examples are polythene and Buna-s, respectively.
- Condensation polymers: These polymers are formed by repeated condensation of tri or bifunctional monomeric units. In this reaction, the elimination of some small molecules, like water and hydrogen chloride etc., will take place. Terylene and Nylon 6,6 are examples.
Based on Forces between Molecules
They are again classified into four subgroups.
- Elastomers: Polymers that are rubber-like solids and have elastic properties. Here, the polymer bonds are held together by weak intermolecular forces and that allows these polymers to stretch. The cross-links present in the polymer between the chains help to retrace the original position after the removal of the applied force. Examples are Buna-s and Buna-s.
- Fibres: They are polymers having strong intermolecular forces like hydrogen bonding. Due to this strong force, molecules are kept closer, that is, they are closely packed. Because of this property, they are crystalline in nature. Polyamide and polyesters are examples.
- Thermoplastic polymers: These are the liner or slightly changed to branched polymers that can be softened on continuous heating and hardened on cooling. Their intermolecular force lies in between the fibres and elastomers. Polyvinyls, polystyrene etc., are examples of thermoplastic polymers.
- Thermosetting polymers: These polymers come under the category of heavily branched or cross-linked, which can mould on heating and can’t regain the original shape. So, these cannot be reused. Bakelite is an example.
Biomolecules and Polymers
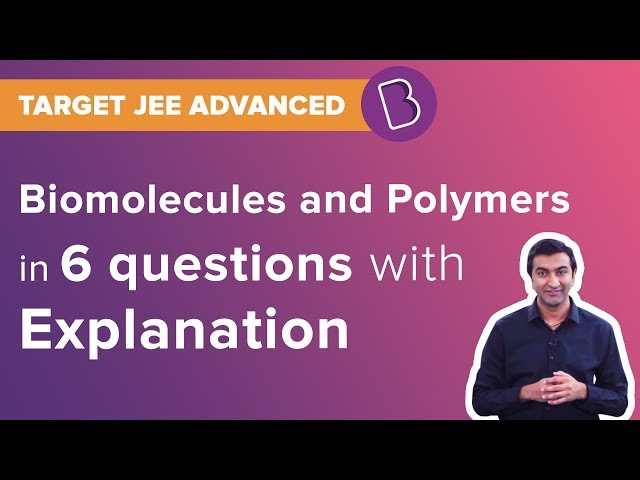
Comments